By Dejan Radosavljevic, Marine Director, Siemens
Reading about and watching images of increasingly frequent extreme weather events it is difficult to keep on ignoring the warnings of environmental change. At the same time the human population continues its rapid increase and utilises more energy and therefore creates greater greenhouse gas (GHG) emissions for daily living.
The consumption of that energy has its negative side in the shape of harmful emissions affecting, one way or another, everyone on the planet. As the consumer driven industries slowly reach a plateau in terms of attainable efficiencies the focus has switched to industries with less direct consumer focus, such as maritime transport.
Maritime is, in absolute terms, a large contributor to global GHG emissions, including SOx and NOx. As a result, pressure is building on the maritime sector to design, build and operate ever greener and cleaner vessels.
Underlying all the requirements for cleaner and greener ships is one fundamental fact that comes before anything else: we need to design ships that are as energy efficient as possible. In cases where carbon-based fuels are still prevalent, it will help minimise emissions, and for renewables and new technologies it will make it easier to satisfy demand with low-density energy sources whatever they may be. For example, maximum efficiency is implicit in the initiative just announced by four Japanese companies that have teamed up to build the world’s first zero-emission tanker by mid-2021, which will be powered by large-capacity batteries.
Simulation Driven Ship Design (SDSD) will offer the maritime industry a new way to design ships such as the Japanese tankers that is quicker, cheaper and achieves better results in terms of vessel efficiencies. But to understand SDSD it is first necessary to understand the status quo.
Design processes are not fit for purpose
Current ship design is a very complex and time-consuming process. Over a century of rule-based requirements have made it a highly rigid, labour intensive process. The rule-based focus, stemming from the need for vessels to survive the harsh sea environment before the advent of GPS, satellite technology and weather routing, meant by far the largest focus was on structural design.
Even today little has changed from the required focus on rule compliance, the effort to go through model testing, the basic and detailed structural design, to time-consuming plan approval of the drawings. Modern technology is helping speed up some of the elements of this procedure, but it is fundamentally still the same time-consuming design process from 100 years ago.
That process creates many problems: for example, the initial tender phase time is very limited and proposing a hull design that minimises capital expenditure (CAPEX) during build, whilst meeting operational expenditure (OPEX) and efficiency demands of the customer, as well as certification requirements, remains a challenging task. One way to reduce the challenge is to use an off-the-shelf design (OTS), which may not be the most efficient design for a different specification. Even if the OTS design belongs to a similar specification the opportunity for innovation to maximise efficiency is gone.
In previous times, when energy was cheap and environmental impact of little concern, these design inefficiencies did not matter. In the last ten years, with oil price increases and global economic uncertainties, these potential design flaws can make the difference between success (and continued orders), and failure. The impact on the shipping business is striking: the number of active shipyards (defined as a yard that has at least one unit of 1,000+ GT on order) has declined by 65% over the past nine years, to only 330 globally, representing its lowest level on record. It is time to establish a ‘new normal’ for marine design.
The ‘old marine normal’ is holding us back
The ‘new normal’ was the subject of the talk by the keynote speaker Nancy Rademaker at last year’s Siemens Simcenter conference in Prague. Rademaker used cassette tapes as one example of the ‘old normal’ – something which was the standard once but has now been replaced by the ‘new normal’, streaming. Music, like many things, is now digital (see figure 1). This is the new normal, and younger generations have no interest in or understanding of the old normal. But what is the old normal in the marine industry, and how can we move to a new normal?
Marine design methods have not really changed in over 100 years. While the industry has at least progressed towards using computer aided design (CAD) models instead of line drawings as standard practice in vessel design, there is continued insistence and reliance on confirming each design suitability via towing tank testing of a physical scaled model.
The limitations of towing tanks are well known, translating model-scale measurements to full-scale vessels is open to many uncertainties and requires the use of empirical scaling formulae. In addition, due to the differences in the Reynolds number, that is the measure of how turbulent the flow is, it is difficult to study interactions between key components accurately such as propellers, appendages, and hulls, or understand performance under dynamic events such as crash-stop or manoeuvring in waves.
Dependence on this limited, expensive and time-consuming method is one aspect holding the industry back from innovating in design and efficiency. This was recently exemplified by Wärtsilä in their recent presentation at the Royal Institution of Naval Architects conference on propeller design, where they showed how they could have ended up with much higher power requirements (and hence much higher emissions) had they followed towing tank test results.
Instead they put their trust in virtual performance prediction using full scale simulation technology, which showed that an alternative design was better, and convinced the owner to trust their results.
The ship was built, and trials confirmed the simulations were correct. One wonders how many of these examples would exist and how many more efficient ships would be in operation today had designers used and/or had the courage to trust simulations to build vessels rather than relying on false readings from model tests.
While it is the major stumbling block, model testing is far from the only issue sustaining the ‘old normal’ for vessel design. Other clues can be found in the name: the ship design process is often referred to as the ‘ship design spiral’, as shown in Figure 2. Just by looking at it one gets the feeling of inefficiency, with multiple iterations over many different specialisms (often siloed in different teams, with little cross-communication). This design process is unwieldy and inefficient, especially when compared with modern design processes in other industries including automotive and aerospace.
The disparate tools used for each step in the design process and the break of the workflow into siloes mean that more detailed analysis does not follow every design change: the expression running in circles springs to mind. And the later the change happens in the design process the bigger the negative impact it will have on the overall cost as well as reduced scope for any design improvements.
The lack of flexibility in this ‘old normal’ design approach only increases the risk to the shipyard, hence the tendency to rely on OTS designs as a conservative approach to ensure profit margins and reduce risks.
A new approach to vessel design is needed and the model for that new methodology has been available for some time.
Meeting the challenges
Luckily, other industries have shown the way it can be done. To start with we need to streamline the design process, get rid of the spiral and combine all the steps together to allow them to interact with each other seamlessly. We also need to move the decision-making process on fixing the design as early as possible, when there is the greatest flexibility to make changes and impact the performance. This approach requires full confidence in predicted performance, which cannot be achieved with continued reliance on model testing.
To achieve all this, we need a fully integrated ship design environment, rather than the current disparate tools and processes. Newport News president Matt Mulherin estimated that applying an integrated approach achieved savings of 15% on the design costs of the third Ford-class aircraft carrier. That is a huge amount of money considering the estimated cost of one vessel at US$13 billion. Even looking at the lower costs for standard commercial vessels, every 1% of cost savings could still save over US$1Million per vessel for larger and more expensive ship types, such as LNGs.
Talking about disparate processes one must also consider many different computer aided engineering (CAE) type analysis applied to assess various aspects of performance. Despite advances in technology, a surprisingly large number of analysts involved in the ‘design spiral’ still use a highly manual approach to testing the performance of a design. This would most often be to validate existing designs or troubleshoot design flaws late in the product development process.
In the case of a detected underperformance the process would be repeated, starting by modifying the CAD model and so on … back into the spiral. For today’s requirements this is a highly inefficient, unreliable way of designing a ship that is simply not fit for purpose. Instead, today there is a much better way of doing it by utilising a fully automated design environment. Combination of parametrisation, automated meshing, templatisation and full process automation (pipelining) allows us to repeat as many simulations as we want by simply changing any of the parameters following a prescribed pattern, and once all the simulations have completed we can look at the consolidated results.
The final ingredient to help achieve better designs is utilising the latest development in intelligent algorithms that apply computer power to seek defined objectives on behalf of engineers. This still seems to be a surprisingly underused element of modern technology within ship design considering the verified capabilities of computers to beat the best humans in their respective fields of expertise when it comes to dealing with complex problems.
Designing a ship is a complex task so we must allow computers to do the heavy lifting for engineers and do the most time-consuming and difficult elements of the work. Computers can seek the best possible designs and only evaluate those that come on top after hundreds and thousands of variants have been checked, rather than basing everything on one OTS design. This way engineers can focus on engineering and innovation, rather than building and running simulation models.
Simulation-driven ship design
When we combine integration, automation and intelligent design exploration with full scale vessel simulation under realistic operating conditions we have the virtual digital framework in place to perform Simulation Driven Ship Design (SDSD), which will, with time in the author’s opinion, completely replace the ‘design spiral’ as we know it. A simplified graphical representation of the SDSD concept is shown in Figure 3. At the centre we have the ‘single source of truth’ – a ship Master Model that can contain any or all the information about any aspect of vessel performance or design needed, from General Arrangement, to Structural Design, to Marine Systems and so on.
All these different representations can be pushed through the simulation in various combinations depending on how all-inclusive a scenario we want to target. What it is key to understand is that simulations allow perfect comparative assessment like no other method could do. By seeking to maximise efficiency or minimise power requirements we are just looking for a design that is better than another.
If we let the SDSD process do that hundreds or thousands of times we will always end up with the best possible design within the specified constraints. Other methods that target a single performance point and rely on a handful of analyses or model tests can never achieve the same outcome. And that is why we need urgently to adopt this ‘new normal’.
The SDSD concept makes the design and build processes flexible and agile and able to respond at short notice to any changes in regulations or requirements. It also makes it possible to meet both environmental requirements as well as owners’ requirements for their vessels to be future proofed against expected further changes in the regulation with a faster shift to alternative energy sources, such as hybrid or battery power. In short – it enables innovation.
Towards a marine digital twin
As the Master model progresses through virtual production, actual production and operation it slowly grows into a true Digital Twin with the full scope for utilising its benefits. Allowing the real time feedback of operational data through the laid out digital thread owners can quickly test multiple ‘what if’ scenarios: what is the impact on safety and performance of the damage or adverse weather conditions? What if we re-design part of the hull? What if we re-purpose the vessel to alternative routes? What if we change to a new engine?
If SDSD and a full digital twin sounds too far-fetched to you, consider: even ten years ago would you have predicted that you would stream music from the cloud? And yet, that is the new normal today. With all the challenges that it is facing, the marine Industry needs to shift away from the ‘old normal’, designing ships using the Design spiral, and embrace the power of digitalisation to make Simulation Driven Ship Design the ‘new normal’.
Siemens already has in place the necessary technology framework to manage Simulation Driven Ship Design and all the tools required to use this approach today. Interest is growing in many companies in ways to make this process a reality: The only question is when will we come to accept it as standard?
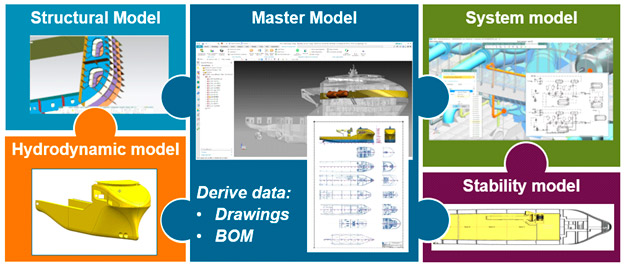